Настольные 3D принтеры
Самые частые проблемы при печати на 3D принтере и способы их устранения
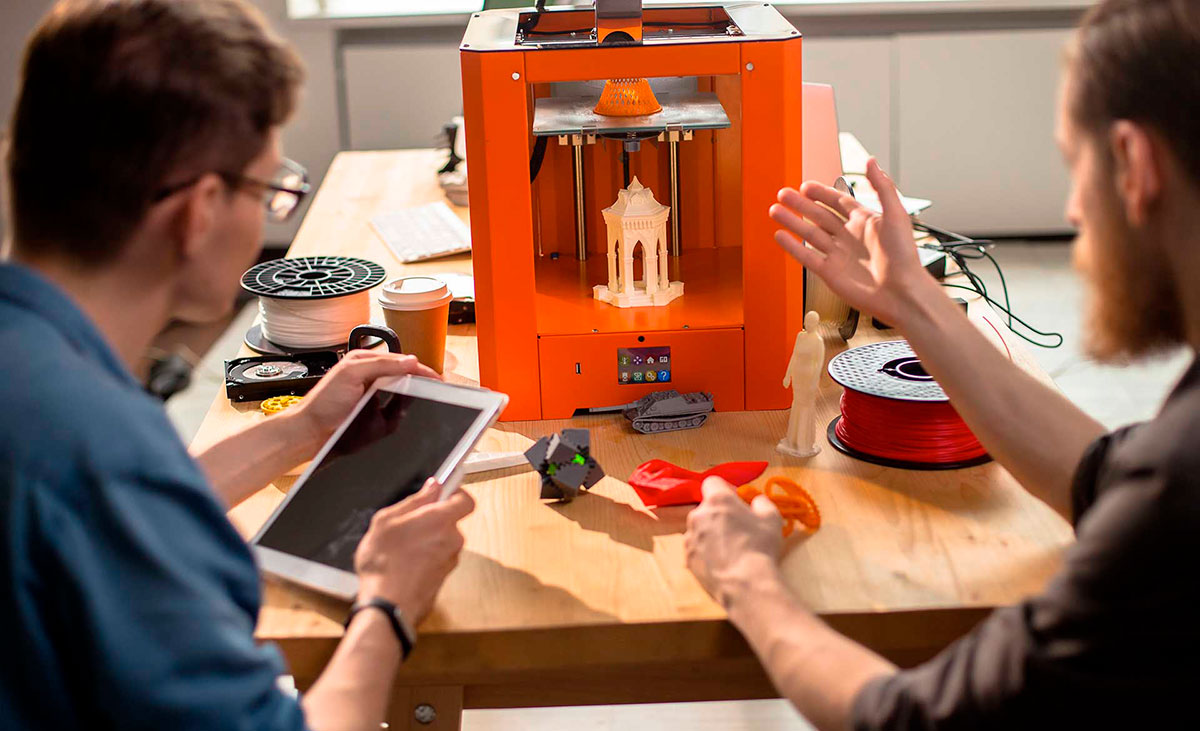
Приобретая устройство для объёмной печати, пользователь рассчитывает получить агрегат, с помощью которого легко и быстро можно будет производить те или иные предметы. Однако всё не так просто: чтобы получить качественное изделие, требуются не только навыки моделирования, но и непосредственно производства. Неправильное положение стола или экструдера, настройки подачи, подогрева или охлаждения филамента могут привести к появлению множества деформирующих элементов, в результате которых модель будет не просто неэстетичной, но откровенно бракованной. Эта статья посвящена разбору проблем при печати на 3D-принтере, а также поиску их решений.
Отсутствует подача филамента
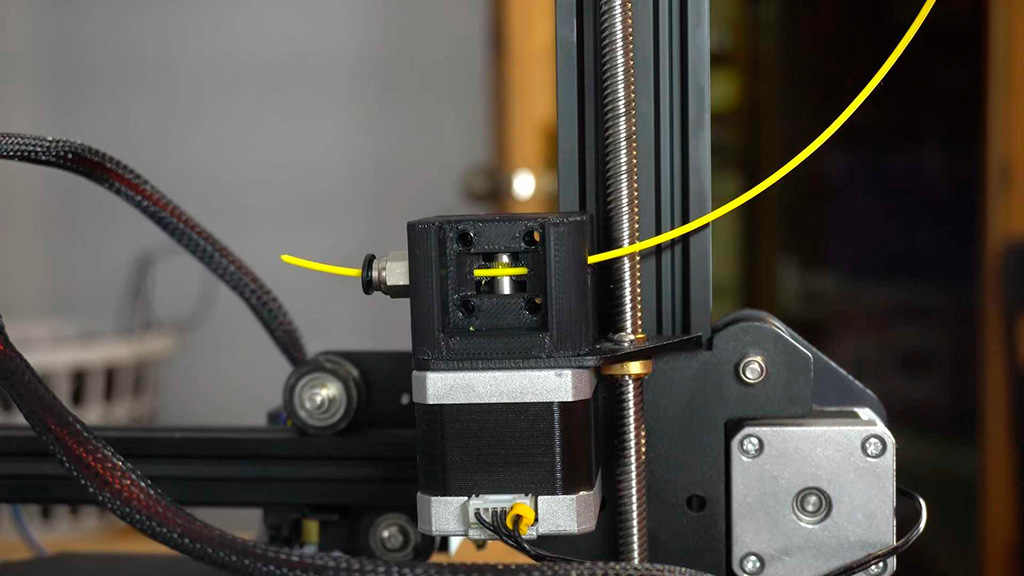
Закончилась нить на катушке
Для моделей принтера с внешним расположением катушки эта проблема очевидна и легко решаема. Но есть модели, где катушка установлена внутри. Некоторые из них оснащены датчиком, информирующим о том, что нить закончилась, на других его нет. Поэтому при отсутствии подачи пластика первым делом проверьте его наличие.
Сопло находится слишком близко к поверхности стола
Если расстояние слишком маленькое, то стол просто физически препятствует выдавливанию нити. События могут развиваться по нескольким сценариям:
- пластика не будет только на первом слое;
- пластик не будет прилипать на последующих слоях;
- произойдёт перегрев и в сопле образуется пробка.
Решить проблему можно путём регулировки высоты стола. Для этого надо увеличить смещение по оси Z до положительного значения. Также можно попробовать просто опустить стол. Но тогда придётся провести повторную калибровку и выравнивание.
Забито сопло

Причин может быть несколько:
- остатки нити от предыдущего мотка в канале;
- образование нагара на стенках канала в результате плохого технического обслуживания;
- частый переход с одного материала на другой без очищения сопла.
Для очистки сопла есть несколько методов:
- механический с помощью тонких острых предметов;
- химический – погружение сопла в раствор ацетона;
- проталкивание специальным чистящим филаментом.
При механической очистке следует выбирать инструмент диаметром меньше канала сопла. Предварительно сопло надо разогреть и затем аккуратно выковырять пробку. Этот метод не слишком эффективен и может повлечь повреждение внутренней поверхности металла. Лучше отсоединить весь экструдер и прочистить его ацетоном или другим растворителем.
Обрыв прутка
Такое чаще случается в аппаратах с Боуден-подачей, где нить не видна, поскольку спрятана в трубке. Нитка может оборваться из-за перетяжки в экструдере. Но причиной также может быть низкое качество сырья или его неправильное хранение, которое привело к снижению качества (например, нити становятся хрупкими при длительном нахождении под прямыми лучами солнца).
Чтобы снизить количество аварий по данной причине, используйте только высококачественное сырьё. Если пруток всё же оборвался внутри, надо:
- Удалить нить из принтера.
- Вытащить трубку из экструдера и шланга хотэнда.
- Нагреть сопло и удалить остатки пластика.
Теперь можно вставить другой вид филамента. Если пруток снова оборвётся, надо ослабить прижимной ролик рабочей головки.
Первый слой не прилипает к столу (отсутствие адгезии)
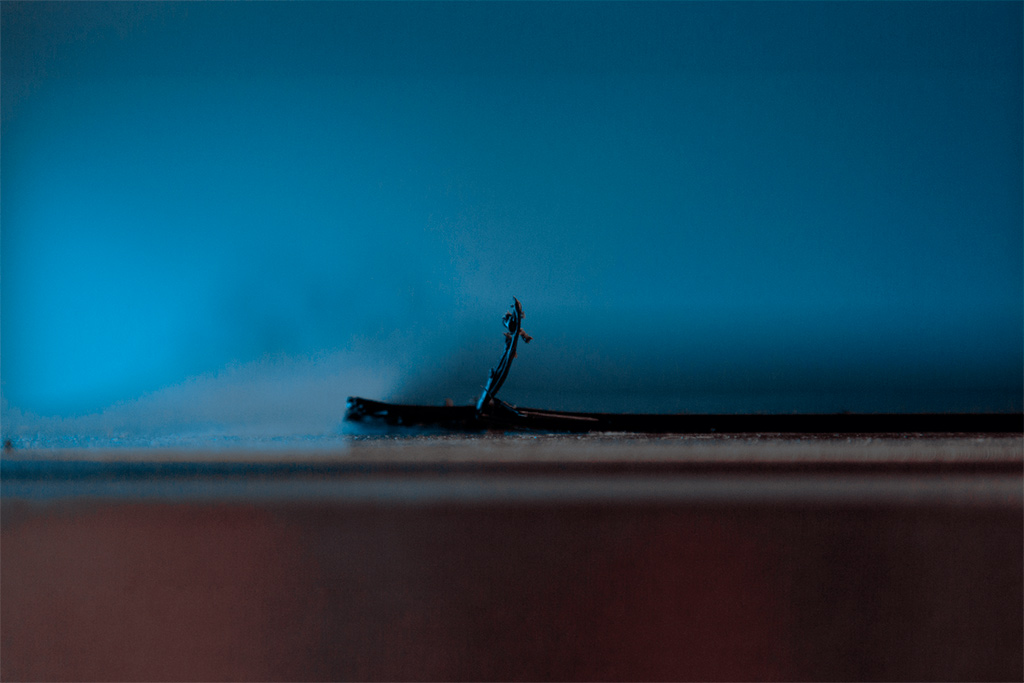
Это наиболее распространённая проблема при печати на 3Д-принтере. От того, насколько прочно прилипнет первый слой, во многом зависит качество модели. Он должен прилипнуть намертво. При слабой адгезии модель может оторваться не сразу, а на середине работы или даже когда будут допечатывать последние уровни.
Причин несколько:
- Стол закреплён неровно. В этом случае в разных точках расстояние между поверхностью стола и выходным отверстием экструдера неодинаковое, что и становится причиной отсутствия адгезии. Чтобы исправить положение, требуется откалибровать положение стола. Если у модели имеется опция автокалибровки, выравнивание упрощается. Если такой опции нет, то выровнять поверхность можно вручную, воспользовавшись винтами. Также можно использовать рафт – несколько слоёв подложки, которые печатаются перед нанесением первого слоя. Рафт поможет справиться с небольшим искривлением рабочей поверхности стола. Ещё один эффективный вспомогательный элемент – брим («юбка»). В отличие от рафта, брим представляет собой прибавочный слой по краю нижнего уровня модели, за счёт чего увеличивается площадь контакта с рабочей поверхностью. Во время печати брим усиливает адгезию, а после завершения процесса удаляется.
- При печати первого слоя сопло находилось слишком далеко от стола. Здесь также понадобиться калибровка.
- Низкие адгезивные качества исходника. Например, нейлон и ABS-пластик обладают высокой усадкой, что часто становится причиной плохой прилипаемости первого слоя. Такие материалы неравномерно остывают: нижние уровни уже остыли, в то время как верхние остаются горячими. Для работы с такими материалами рекомендуется использовать печатающее устройство с подогреваемой рабочей поверхностью и закрытым корпусом.
- Недостаточная температура разогрева нити. Материал не достигает стадии расплавления, при которой может прочно прилипать к поверхностям. Предотвратить проблему можно, подняв на 5-10°С температуру при производстве первых нескольких слоёв и одновременно отключив охлаждение.
Образование «паутины»
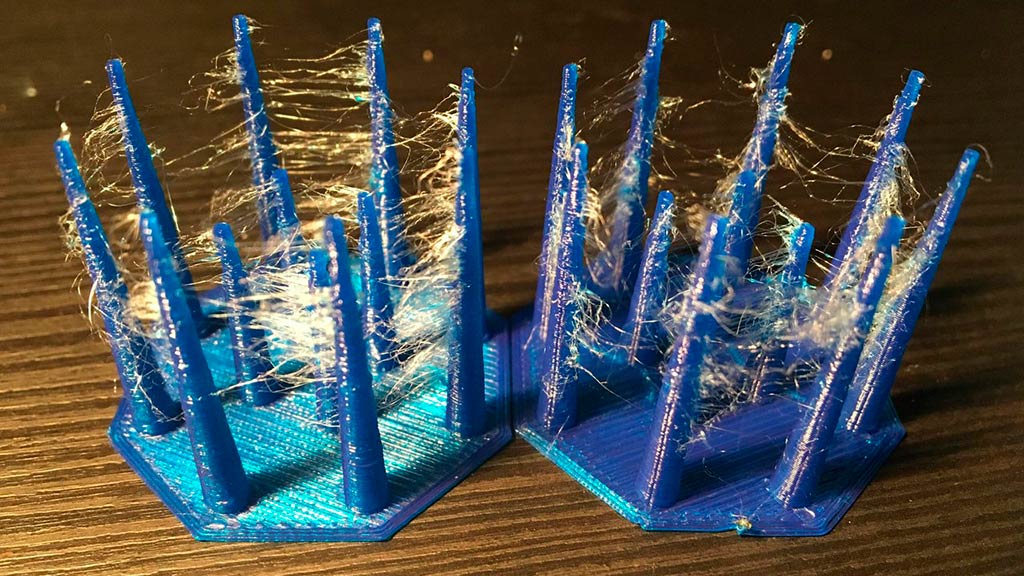
Визуально это выглядит как множество мелких волосков на внешней стенке готового изделия (обычно с одной стороны). Причина дефекта – вытекание материала на холостом ходу. Ретракт – это опция, при которой создаётся незначительное отрицательное давление в сопле, благодаря чему происходит эффект втягивания прутка и он не вытекает на холостом ходу. Паутина начинает образовываться тогда, когда дистанция ретракта слишком мала. Увеличив её, можно избавиться от «волосатости» поверхностей готовых изделий.
Модели с эффектом паутины не считаются испорченными, поскольку его можно удалить при помощи шлифовки.
Среди других причин образования волосков выделяются:
- низкая скорость ретракта;
- слишком высокая температура сопла, из-за чего происходит подтекание;
- большая скорость экструзии.
Все эти причины легко устраняются отладкой настроек.
Расслоение (плохая когезия)
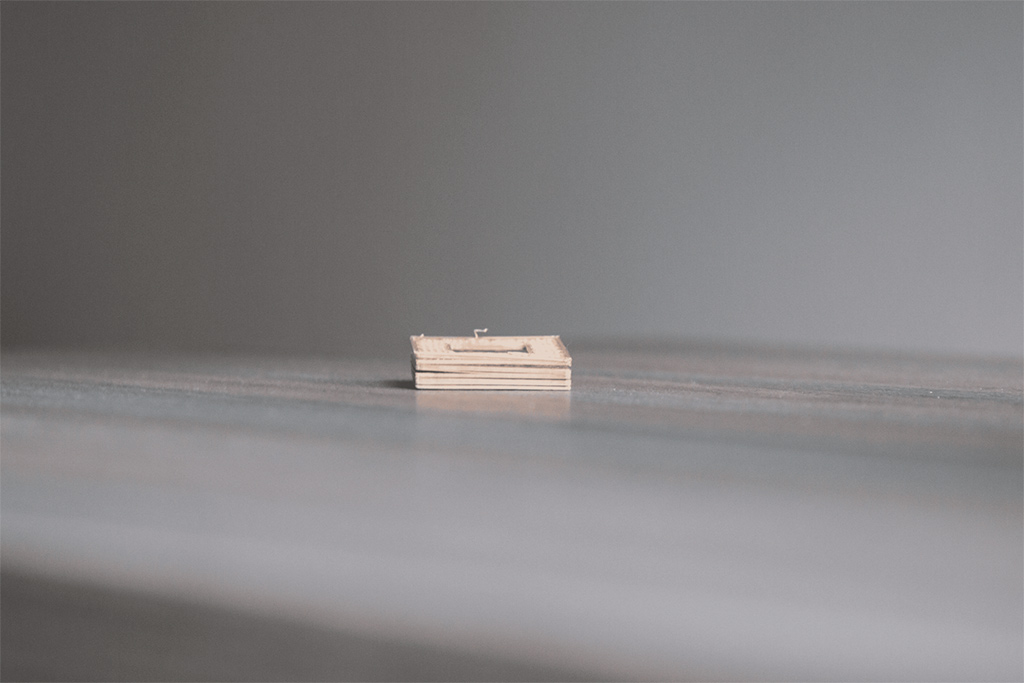
Расслоение может появиться как сразу после окончания печати, так и через несколько дней. Независимо от размера трещин (незначительных или больших) модель отправится в брак. Расслоением чаще страдают изделия, выполненные из материала с повышенной усадкой. Поэтому при работе с ними надо более тщательно проводить настройку процесса, а также учитывать внешние факторы:
- Плохая когезия может быть результатом низкой температуры в камере: материал просто не достигает состояния, при котором склеивание становится прочным.
- Низкая температура сопла также является причиной плохого склеивания слоёв.
- Пониженный коэффициент экструзии не позволит слоям надёжно спекаться.
- Толщина слоёв. Она должна составлять не более 75% от диаметра сопла. Большая толщина приводит к снижению когезии.
- Резкое охлаждение, например в результате сквозняка, приведёт к неравномерному остыванию, усадке, нарушению распределения внутреннего напряжения и, как следствие, расслоению. Для работы с материалами, обладающими большой усадкой, лучше использовать печатающее устройство с закрытой камерой. Если же рабочая платформа открыта, то следует позаботиться о том, чтобы температура в помещении была достаточно высокой, а также исключить возникновение сквозняков. Охлаждение должно быть не быстрым и равномерным. Каждый уровень должен достаточно остыть перед нанесением следующего. Для каждого вида пластика разработаны свои параметры, которые нельзя нарушать.
Если трещины появились спустя некоторое время, при этом они не критичного размера, можно попробовать закалить изделие в духовом шкафу. Для этого надо нагреть духовку до температуры размягчения пластика, поместить внутрь модель, выключить духовку и оставить её внутри закрытого шкафа до полного остывания. Повторный нагрев поможет склеить появившиеся трещины, а также перераспределить внутренее напряжение, чтобы они не появились вновь. Однако это способ требует осторожности: если температура окажется слишком высокой, изделие «потечёт».
Деформация формы углов

Уголки конструкций могут заворачиваться внутрь (отлипая от стола) или, утолщаясь, расплываться, образуя так называемые «слоновые ноги».
Закручивание внутрь чаще всего происходит при остывании и сильной усадке пластика. Дополнительный подогрев стола задержит остывание и не допустит преждевременного отлипания углов. Другой защитный приём – создание «ушек» – дополнительной структуры, увеличивающей поверхность соприкосновения печатаемой детали с рабочей поверхностью. Ушки – это разновидность брима, они добавляются через настройки в слайсере.
Для усиления адгезии можно использовать клей или лак. Их наносят на предварительно очищенную поверхность.
«Слоновья нога» визуально выглядит как утолщение основания детали. Дефект проявляется по-разному:
- Только в нижнем уровне. В этом случае достаточно скорректировать настройки.
- По всему периметру. Причина, вероятнее всего, в неровности размещения рабочей поверхности. Понадобится калибровка.
- Сразу в нескольких нижних уровнях. Такой дефект является результатом работы с неподходящей температурой. Работа с подогретой поверхностью стола важна для хорошего прилипания. Но перегрев приводит к замедлению процесса затвердевания. Наслоение следующих уровней создаёт слишком сильное давление на нижние и расплющивает их. Исправить положение можно путём:
- снижения подогрева;
- усиления мощности обдува;
- снижения скорости подачи прутка.
Иногда приходится одновременно применять все три приёма.
Также эффективно действуют рафты и компенсирующие фаски для нижнего края.
Сдвиг слоёв
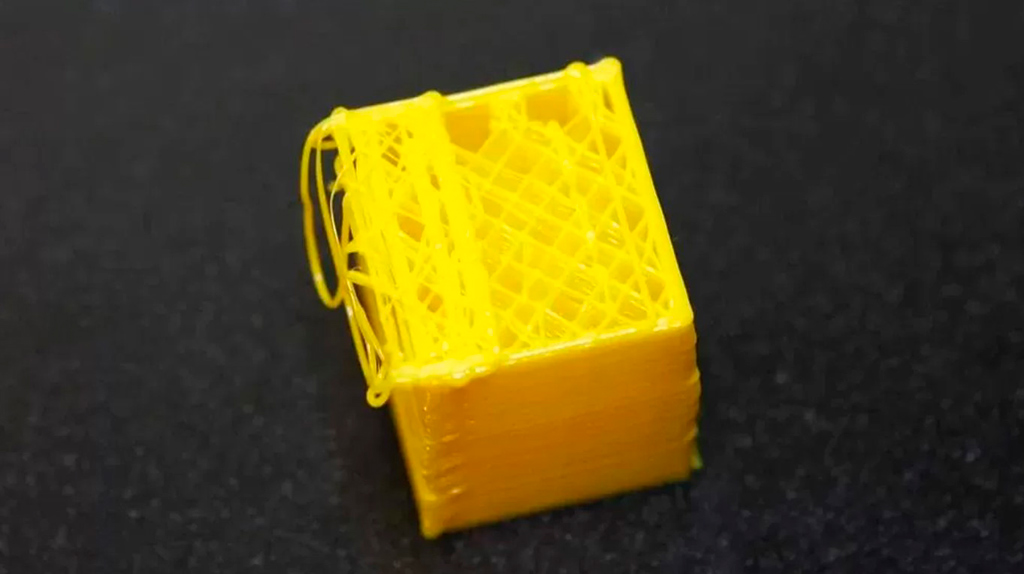
Небольшой сдвиг проявляется в неровности одной из поверхностей. Но бывает и так, что готовая модель напоминает лестницу. Подобные нарушения печати происходят в результате сбоя в механике принтера. Со временем соединения узлов разбалтываются и требуют подтяжки. Если сдвиги появились, надо:
- Проверить натяжение ремней. При сжимании пальцами они должны оказывать лёгкое сопротивление. Если окажется, что сопротивление в верхней части больше, чем в нижней, значит требуется подтяжка. В зависимости от модификации принтера это можно сделать вручную или при помощи встроенных натяжителей.
- Удостовериться, что ремни не скользят по шкиву.
- Проверить направляющие валов. Этот узел со временем накапливает грязь, влекущую за собой целую цепь событий: трение усиливается, скольжение подшипников и втулок ухудшается, слои сдвигаются. Решение проблемы – валы очистить, подшипники и втулки смазать.
- Проверить валы или резьбовые шпильки на искривление. Чтобы обнаружить изгиб, надо снять вал и прокатить его по ровной поверхности. Лёгкие искривления можно выпрямить руками. Искривление шпильки можно обнаружить при помощи соответствующих опций в программе. Если дефект обнаружен, шпильку надо менять.
Обрушение поддержек
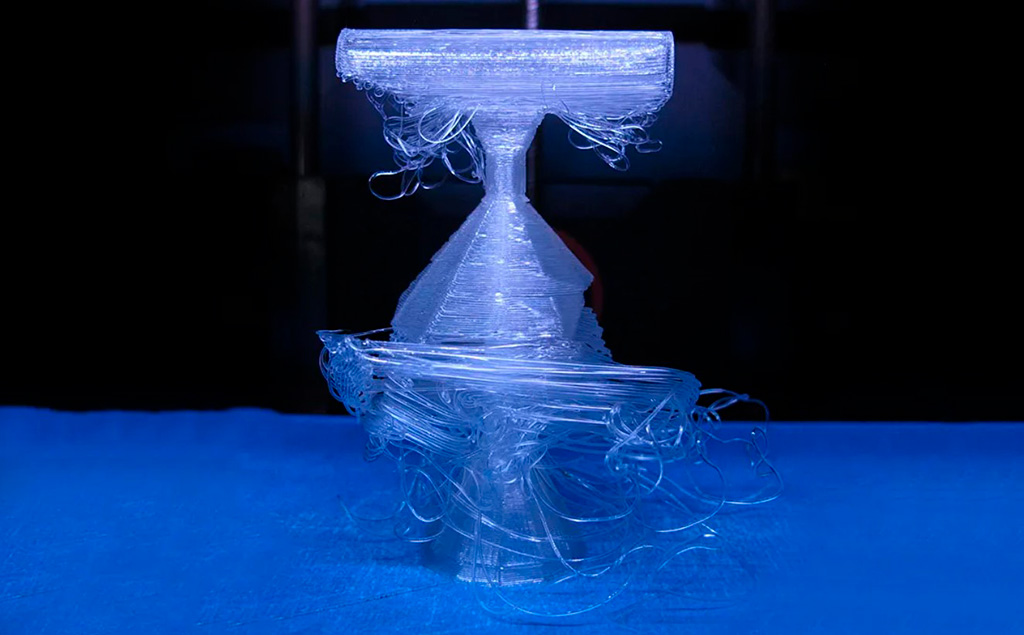
Поддерживающие конструкции необходимы при печати сложных изделий с нависающими частями. Однако работать с ними непросто. Во-первых, они сложно удаляются, а во-вторых, часто портятся во время печати, частично или полностью разрушаются и портят (а иногда и вовсе уничтожают) прототип.
Разработка поддержек – это сложная часть структурного моделирования. Существуют разные типы поддержек. Чем проще конфигурация, тем легче поддержки удалить, тем хуже они выполняют свою функцию. Самые простые виды – это прямые и зигзагообразные стойки. Именно они чаще всего ломаются в процессе печати. Самыми надёжными конструкциями являются сетки.
Если модель слишком высокая, то и поддержки будут чересчур высокими, что также может стать причиной их обрушения. Ещё одна распространённая причина обрушения – минимальная плотность конструкции. Это делают для того, чтобы проще было очистить готовое изделие.
Среди других причин можно выделить:
- низкокачественное сырьё;
- сильную вибрацию принтера во время работы;
- слабую адгезию поддержек.
Решения проблемы:
- Использовать только новый качественный пластик.
- Не допускать вибрации принтера при работе.
- Усилить адгезию поддержек, например, бримами.
- Правильно подбирать вид поддержки, а также для усиления жёсткости создавать конструкции внутри модели.
- Не снижать плотность поддерживающих конструкций.
Отверстия и щели
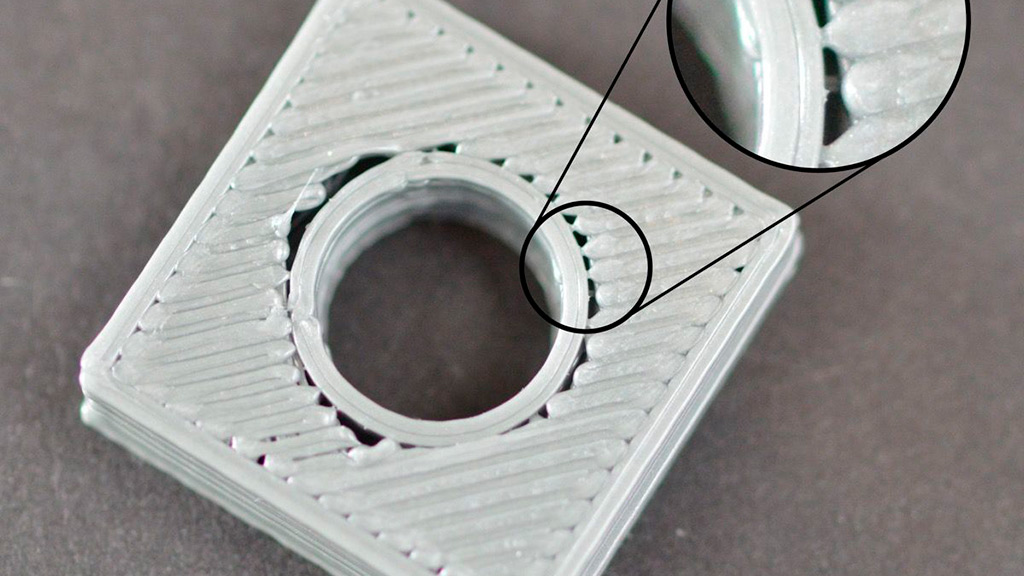
Этот дефект проявляется по-разному.
Щели между стенками. Появляются, если слайсер при делении стенок на линии не получает целого числа. Предположим, что стенка состоит из двух периметров – внешнего и внутреннего. Толщина каждого из них по одному миллиметру, а заданная толщина линий по 0,5 миллиметра. Сумма двух линий составляет 1 миллиметр, что и требуется. В этом случае щелей не будет. Но если толщина линий окажется, например, 0,4 мм, то сумма получится 0,8 мм, а оставшиеся 0,2 мм превратятся в щель. Чтобы не допустить образования щелей, можно:- заменить сопло на другое с большим диаметром;
- увеличить значение потока, чтобы материал при подаче вынужден был немного расплющиваться, заполняя тем самым пустоты.
- недостаточная мощность обдува: нити не успевают просохнуть и затвердеть, в результате чего обрываются, образуя отверстия в крыше;
- недостаточно верхних слоёв: крыша получается тонкой и проваливается;
- низкий процент заполнения: «крыше» будет не на что опереться, и она частично или полностью провалится.
Недоэкструзия и переэкструзия
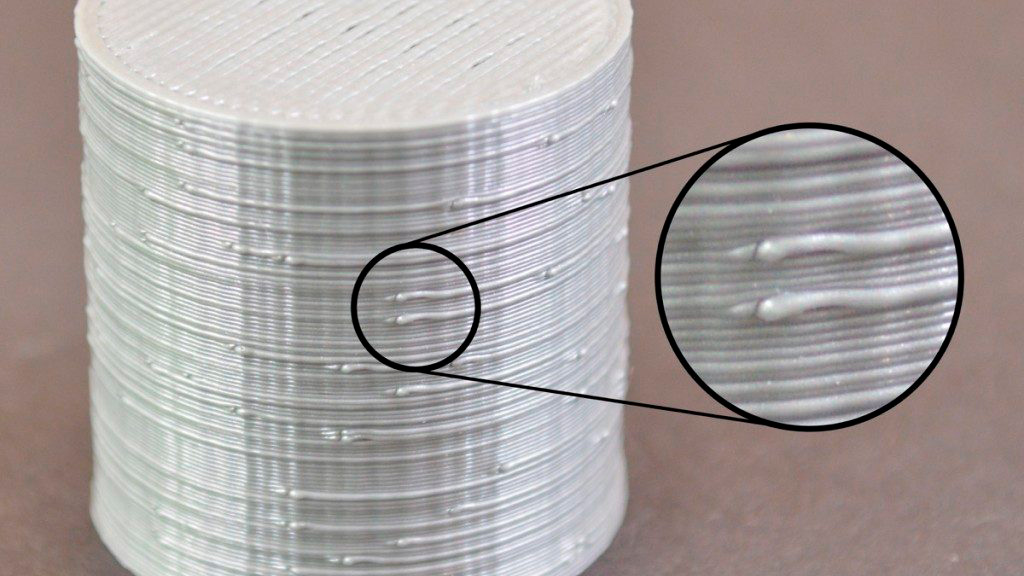
Чрезмерная или недостаточная подача пластика вызывает дефекты поверхностей. Если материала слишком много, поверхности будут неровные с наплывами и буграми. Стандартное значение коэффициента подачи материала 90-95%. Если текучесть явно избыточная, то следует уменьшить её процентный показатель в настройках.
Причинами недостаточной экструзии может быть засор сопла, мешающий выходить прутку, неправильный его диаметр, а также неподходящее значение коэффициента текучести. Результат недоэкструзии – щели между пластами, высокая хрупкость готовой модели. С решением вопроса всё просто, надо:
- проверить выходное отверстие рабочей головки, при необходимости прочистить;
- отрегулировать значение коэффициента текучести (увеличить);
- проверить соответствие диаметра прутка.
Нестабильная подача расплава
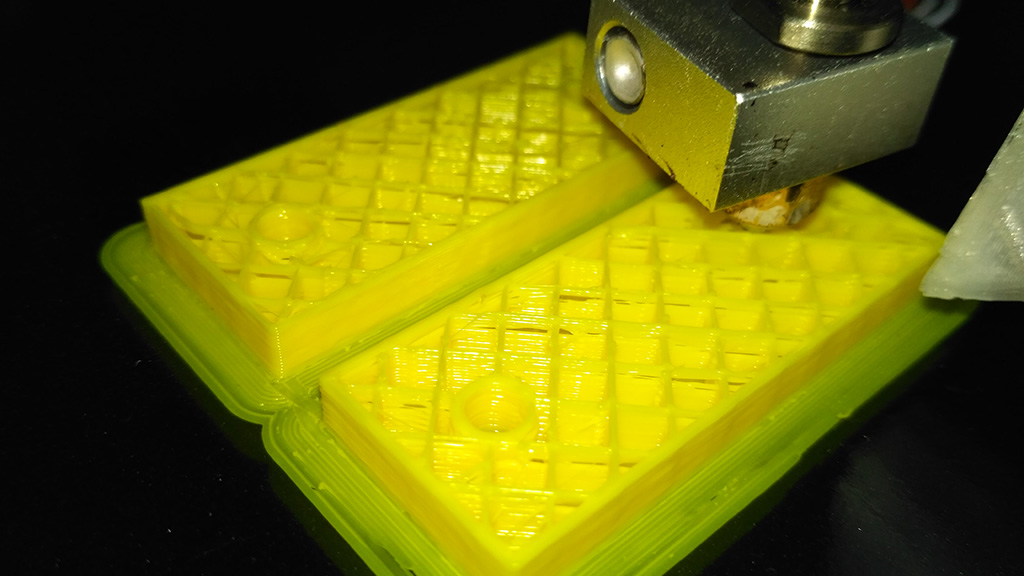
Нестабильность экструзии приводит к неоднородности поверхностей изделия. Причиной может быть:
- Неправильно выставленная толщина слоя. Чтобы укладка нитей была ровной, а склеивание прочным, необходимо выставить значение толщины прутка на уровне 75% от диаметра сопла.
- Неподходящее значение толщины линий. Его тоже рассчитывают, отталкиваясь от диаметра сопла. Оптимальная толщина – 1-1,5 от диаметра сопла.
- Загрязнение канала подачи нити.
- Пробуксовка механизма подачи нити. Если скорость подачи прутка будет слишком большой, принтер будет стараться выполнить эту задачу. Однако хотэнд не будет успевать достаточно разогревать материал. Понять, что машина буксует, можно по характерным щелчкам, которые появятся, когда агрегат не сможет проталкивать нужную порцию материала. Если увеличить температуру, пробуксовка прекратиться. Но тогда возникает угроза перегрева, чрезмерного расплавления пластмассы и её нестабильной подачи. Поэтому лучше всего точно соблюдать скоростной и температурный режимы.
Если принтер оснащён трубкой Боудена, то причиной нестабильной подачи расплава может стать её деформация (изгиб).
Перегрев
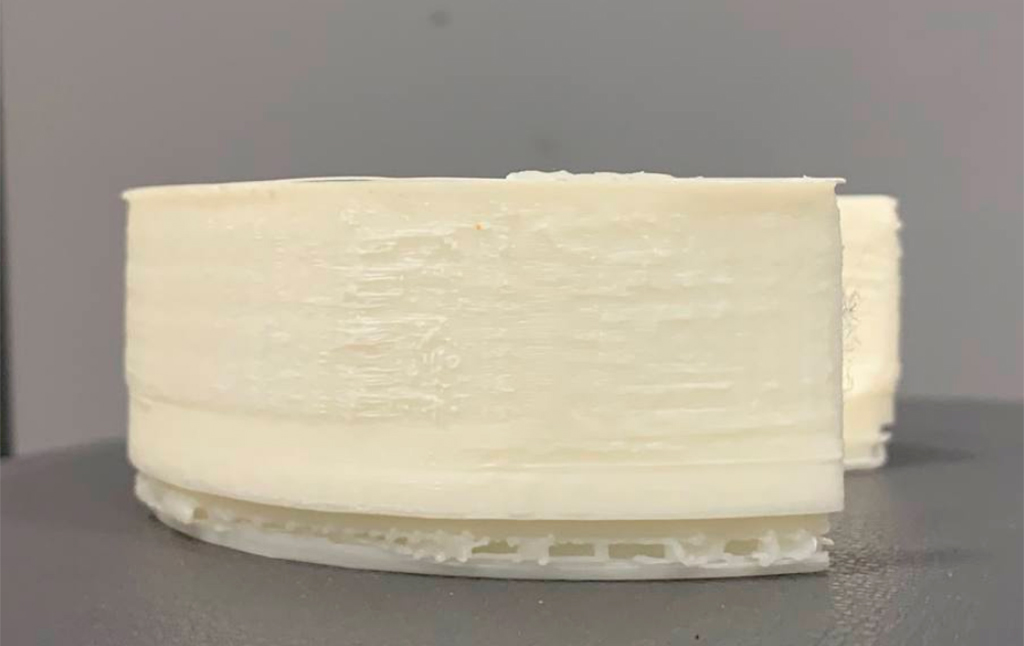
Слишком высокие температуры расплава часто становятся причиной брака на печати. Показателями перегрева пластмассы служат:
- повышенная текучесть материала, который просто выливается из канала и остаётся на стенках изделия в виде подтёков;
- поверхность модели становится волнообразной;
- наблюдается дым при выходе расплава из сопла.
Факторы, приводящие к возникновению перегрева:
- Недостаточное охлаждение. При этом у каждой марки пластмассы свои параметры разогрева и охлаждения. Например, ABS-пластик разогревается при +80°С, а для работы с PEEK нужна температура не ниже +250 °С. Чтобы предотвратить перегревание, попробуйте увеличить мощность обдува.
- Иногда проблема кроется в повышенной температуре сопла. Достаточно её уменьшить, и печать пойдёт в штатном режиме.
- Высокая скорость печати препятствует охлаждению. Уровни не успевают затвердеть и начинают деформироваться.
Подводя итоги, можно сделать следующие выводы. Основные проблемы при печати на 3D принтере связаны с:
- нарушением температурного или скоростного режима работы аппарата;
- загрязнением канала, по которому подаётся расплав, а также выходного отверстия;
- нарушением настроек;
- ошибками при моделировании;
- нарушениями работы механических частей.
Регулярное техобслуживание поможет избежать проблем с загрязнением или плохой работы механических конструкций. А тщательное моделирование и соблюдение параметров работы с разными видами пластмассы не создаст трудностей при печати.